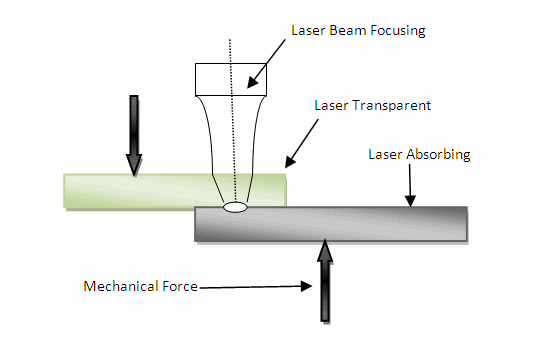
|
Figure
1 – Through Transmission Laser Welding of Plastics |
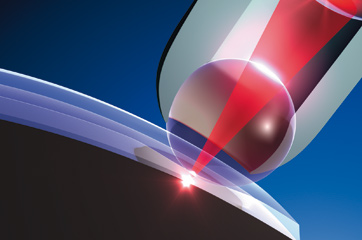
|
Figure 2 –
Globo Laser Head
(Courtesy Leister Technologies)
|
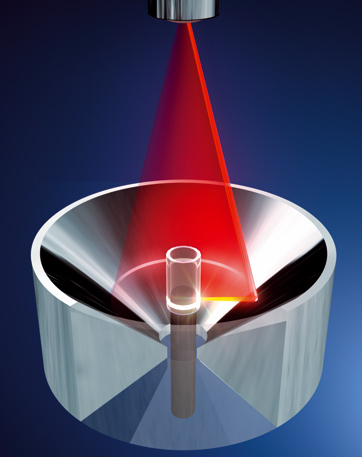
|
Figure 3 –
Radial Welding Fixture
(Courtesy Leister Technologies)
|
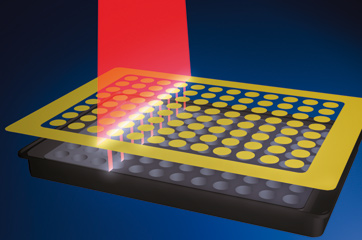
|
Figure 4 –
Masking System
(Courtesy Leister Technologies)
|
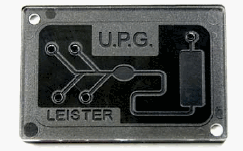
|
Figure 5 –
Microfluidic Device
(Courtesy Leister Technologies)
|
The use of near infrared lasers to weld plastics has been increasing steadily over the past few years. This technology has been advanced by the introduction of novel laser absorbing materials and by improvements in the design of lasers in plastic welding operations. Diode and Nd:YAG lasers have been used to join thermoplastic components for a number of years. And recently the use of fiber lasers has become significant in this process. All of these lasers rely on the through transmission laser welding technique (Figure 1). That is, the laser radiation passes through a “laser transparent” upper layer and is absorbed by a “laser absorptive” lower layer. The absorbed radiation is converted into heat near the interface of the two layers. The heat is conducted from the interface to the upper and lower levels causing the two layers to melt and flow together to form a weld.
Since thermoplastics generally transmit light in the infrared energy range, the welding process requires the use of an additive that will absorb infrared energy. Carbon black can be used as an infrared energy absorber in a wide range of laser welding applications. This system works well since carbon black is both inexpensive and absorbs energy at any wavelength. Its major drawback is that it introduces a dark coloration to the parts, which is objectionable in applications that require transparent or lightly colored components.
A second method of increasing the infrared absorption of plastics is to add an organic absorber to the plastic. A system that enables the welding of transparent or opaque plastic materials was developed by TWI Ltd in conjunction with Gentex Corporation. The process utilizes organic-based near infrared absorbers as coatings on polymers or as additives to resins. Since the commercialization of this system under the Clearweld® brand name, companies such as BASF, Merck, Orient Chemical, and Fuji have developed laser absorbing additives for use in laser welding of plastics.
Infrared absorbers can be directly incorporated as additives into the plastic during extrusion and molding operations. These additives are formulated for use with specific types of lasers. The absorber is selected so that its maximum absorption wavelength matches the wavelength of the laser used in a specific application. Once the plastic contains the absorber, the welding process is similar to that used with carbon black welding. However, the use of infrared absorbers facilitates more color flexibility. Ideally the additives have high absorptions in the near infrared range and low absorptions in visible range of the electromagnetic spectrum. As with carbon black welding one of the parts serves as a heat sink while the other part transmits the laser energy.
The absorbers also can be incorporated into thin films. These films can be placed between two substrates and used to create a weld joint when exposed to an infrared laser. Additionally, the material can be insert-molded into other parts.
Some absorbers also can be applied as a coating to the surface of one of the parts at the weld interface only. The coating absorbs the laser energy and converts it to heat energy. This allows the plastic on either side of the surface interface to flow together to form a weld joint. The coloration of the coating is dissipated in the reaction, thereby permitting the formation of a transparent weld joint. As this occurs, the ability of the absorber to convert infrared light to heat is lost and any additional infrared energy is transmitted through the lower layer. This results in a relatively small heat affected zone adjacent to the weld.
Laser welding has become more significant in the past couple of years as understanding of the technology increases. Smock recently indicated four factors for accelerated interest in laser welding as a method of joining plastics1. The first is that major resin companies are expanding materials choices for laser welding of black and other color plastics. Second the comfort level with the technology is increasing among design engineers. Third a difficult litigation struggle over patent issues in Europe is being resolved. And fourth, new equipment technology is expanding joining options.
Patent Situation
The development of laser welding technologies has been advancing at a faster rate in Europe than in North America. But one issue that has been detrimental to the commercialization of laser welding of plastics in Europe has been the clouded patent situation. The major issue involved the basic patent for the use of infrared absorbers in laser welding. In January 2003, TWI, Ltd was granted patent 1117502 by the European Patent Office. It was opposed by a large number of companies that were involved in plastics welding. They filed an appeal with the EPO in October 2003, citing a large number of patents and other documents. In February 2005, a patent review board in Germany revoked the TWI patent. TWI then filed an appeal of this ruling. In September 2007, the EPO reversed the result of the earlier appeal. The TWI patent was upheld along with all of its claims.
The intellectual property situation is now clearer. TWI possesses the primary patent for the use of absorbing additives for laser welding of plastics. Gentex Corporation is the sole, worldwide licensee of the TWI patent. However, the marketing of absorber systems has been opened since Gentex has reached agreements with BASF and Merck whereby they can market their proprietary absorbers under the protection of the TWI patent. Gentex has also been granted several patents for laser welding processes in the U.S.
A second area of contention in laser welding of plastics in Europe involved a patent by Marquardt. In 1999 Marquardt received a patent that covered the laser welding of black-to-black plastic parts. The parts had pigments or additives in both parts. The parts had to be of the same color and reflectance and had specified absorbance limits. The resin manufacturers and blenders were curtailed in their entry into the market place by this patent. This obstacle to the expansion of the laser welding market has been mitigated by licensing agreements.
The welding of white parts to white parts is one of the most difficult things to accomplish with infrared laser welders. Orient Chemical (Japan) has developed a system that it claims will accomplish this task. The company has been granted patents for its system in Europe and has applied for patent protection in the U.S.
Commercial Absorbers
The use of lasers to weld plastics is most common in the automotive industry. An early application was the welding of “smart” ignition keys. In order to prevent damage to the solder joints of internal microchips, manufacturers changed from ultrasonic to laser welding. Since the assemblies are black or gray, the devices could be welded by loading the resin with carbon black. Since then, items such as electronic housing, tanks, fluid delivery systems, pumps, and body components have become ideal candidates for laser welding. Laser welding has been used in the assembly of air intake control valves since it provides a smoother weld surface than vibration welding, thereby reducing turbulent airflow. The same concept has been applied to other under-the-hood applications where color is not a critical factor. This technique also has been expanded to non-automotive uses, such as cell phones, electronic enclosures, computer keyboards, and so on. In order to make the plastics laser absorbent, carbon black is added to the resin - generally in the range of 0.05 to 0.5 percent.
Resin manufactures have been developing standard resin packages that are suitable for laser welding. If the top part is laser-transmissive and the bottom part is laser-absorptive, the parts should perform in an acceptable fashion. In order to meet this need, resin suppliers have developed standard laser weldable resins. For instance Bayer offers a PC/PBT blend that absorbs laser light. It has been used in the components of an automobile control system that is joined by laser welding. BASF offers polyamide and PBT as well as several other resins that are suitable for near infrared laser welding. And Du Pont offers black acetal and polyamide for laser applications. These are all for black applications however.
When a manufacturer requires a part that is other than black or gray, it must look at near infrared absorbers other than carbon black. The selection of organic absorber systems available to the end user has become clearer over the past couple of years. These near infrared absorbers were introduced approximately six years ago. Initially they were available as coating systems. Since then a number of absorbers that are tailored to be blended into resins and films have become available.
Lasers
Just as the use of infrared absorbers has been defined, the role of laser manufacturers also has become clearer. The major players in the laser industry have been struggling to develop the laser welding market. Initially most laser companies took existing laser systems and used them for plastic welding applications. A company that had a marking laser quickly converted it to a welding laser. The price advantage of diode lasers, which were widely used as pumping lasers, led other companies to use these lasers as opposed to longer wavelength lasers. But over the past few years, the laser companies have generally opted to concentrate on providing market differentiation for their product line.
There now are well-defined interests in specific wavelength lasers and application techniques. Most laser companies have developed modular and turnkey systems over the past couple of years. The market now can be divided into plastic welding companies (system integrators) and laser suppliers (component suppliers). Plastic welding companies include bielomatik, Branson, Leister Technologies, LPKF, Prolas, Savcor Alfa, and Trumpf.
bielomatik is the leading proponent of Nd:YAG lasers along with the use of quasi-simultaneous (scanning) welding, holding a patent in this field. However, the company’s expertise covers all forms of laser welding. It also has placed a lot of emphasis on the solution of joining problems as plastic joining experts. Through design of fixturing for the welded parts, automated systems have evolved which are optimized for specific applications.
Branson initially developed a laser system that would fit into the framework of its basic ultrasonic welder. The company recently has redesigned its product and now has a more compact product, the IRAM 200 and 300 series infrared welders. It has also focused its efforts on using simultaneous welding techniques as the preferred method of welding. However, Branson is flexible in its designs and can provide alternative systems such as contour and curtain welders.
Leister Technologies has a modular unit, the Novalas Basic AT, and markets a unique laser head, the Globo head, which is shown in Figure 2. This system uses a rotating glass ball to focus the laser beam while applying pressure directly to the part that is being welded. This eliminates the need to apply pressure across the entire assembly. Leister also markets a radial welding technique that is designed for use with cylindrical parts. As shown in Figure 3, the laser beam is reflected off a mirrored surface and directed to the weld area at an acute angle. Leister also has developed a unique masking system in which the mask positioning is optimized by computer control. This system is shown in Figure 4.
LPKF (formerly LaserQuipment) generally uses 940 – 980nm contour laser welding. It markets its laser welder as the LW-Power RT. LPKF also has used the novel concept of “hybrid welding” in one automotive application. It welds a taillight assembly that consists of a clear or red PC lens and a black or gray PMMA housing. The welding is done by a combination of laser welding and infrared radiation. LPKE claims that the weld joint is 1,000 mm in length and that it can be welded in 30 seconds.
Prolas provides modular laser welding machines, which can be assembled according to the needs of each application. It also has developed a hand-held laser system for manual laser welding applications. In addition, its TexWeld Laser sewing machine offers numerous advantages over traditional methods of stitching or welding fabrics.
Savcor Alfa workstations are designed to meet the specific needs of each customer, with standard and custom-built units for stand-alone and in-line production. The company’s experience in laser materials processing and production automation results in products that meet the needs of industrial laser processing and the demands of high volume mass-production.
Trumpf recently has added a laser welding capability by the acquisition of Fisba in February 2008.
Laser companies include Coherent, IPG, Jenoptik, Laserline, Optotools, Rofin, and SPI.
Coherent concentrates its efforts on lower power, compact diode lasers.
IPG is a major supplier of high power fiber lasers. For plastic welding, it offers systems at 1070nm with several hundred watts of power.
Jenoptik Laser Technologies has introduced modular lasers into its product line. The company markets the laser welder as Votan™ W Modular Laser System.
Laserline markets a new version of its diode, scanning laser, the LMD400-200 laser system. This system includes an upgraded software control package that is much more user friendly than its original model.
Optotools offers diode lasers of different wavelength with power up to 300 watts in combination with glass fiber beam guiding systems.
Rofin has marketed contour lasers that are compact in size and easily mounted on standard production robotics. The laser is almost a stand-alone system that can be adapted to various control systems. It also offers scanning (quasi-simultaneous) diode lasers and diode pumped Nd:YAG lasers under the StarWeld Diode brand name. And it offers a turnkey laser system for plastic welding called PolyScan.
SPI is a major proponent of fiber lasers. The company cites the versatility of fiber lasers at 1090nm in laser marking, microelectronic, micro cutting, machining of silicon wafers, and sintered-metal rapid-prototyping.
The marketing of High Power Diode Lasers (HPDL) has been another recent development in the laser welding field. They consist of several small diode lasers that form a laser bus. The laser can be relatively small. One unit is described as the size of a shoebox. However, it can produce 4 KW of power with a life expectancy of 10,000 hours. The beam quality of these lasers is inferior to a single lasers source such as Nd:YAG lasers. Also the beam focus of the HPDL is larger than traditional laser and is rectangular rather than circular, resulting in lower energy density.
HPDL also are available as fiber coupled laser sources. The laser radiation is coupled into a glass fiber which is mounted directly to the laser head. The glass fiber guides the laser beam to the focusing unit and transforms the laser beam into a circular pattern. Depending on the core diameter of the glass fiber and optics, beam spot sizes of less than 1mm are possible.
A good deal of development work on fiber lasers also has occurred. Companies such as IPG and SPI are advocates of this optical system. They are able to produce beam sizes of less than 1mm. Spot sizes as low as 300 microns have been reported. This small spot size allows the laser to produce high energy densities at very low power outputs (1 to 10 watts).
Equipment Selection
With the large number of variables that are present in today’s infrared laser systems, it can be difficult to determine which system is best for each application. Before a laser welder can be used the end product should be evaluated for use with the technology. Questions which should be asked include the following:
- Are the plastic parts miscible and do they have compatible melting temperatures?
- Will infrared absorbers be compatible with the resins?
- What laser source and optics system is best for the application?
- Has the part been designed to minimize gaps and to allow access of the laser beam to the weld joint area?
- What sort of fixturing is necessary to permit laser welding while applying adequate pressure to the part during the welding operation?
High equipment cost is still an issue. Although the price of a typical laser has been reduced as the technology has advanced, it is still a major factor in selecting a welding system. Many laser manufactures indicate that the price of infrared lasers is comparable to that of ultrasonic welding equipment.
An understanding of laser systems is a necessity when considering infrared laser welding. The choice of the laser optical system is often affected by the weld width of the part. Diode, contour welding is preferred for wider lines and complex geometries. Nd:YAG and fiber lasers are preferred for smaller lines widths (1mm or less). And fiber lasers are necessary for very small lines such as in microfluidic applications. For diode and Nd:YAG lasers the power should be in the range of 30W to 150W for most applications. For fiber lasers, lower power levels are suitable since the beam width is much smaller in this system.
Gaps between parts that are to be welded should be 100 microns or less for contour welding. Scan welding permits larger gaps since the beam passes over the entire weld area several times and material collapse occurs to accommodate part variation. As a result the weld zone is heated more slowly and the substrates will have a more uniform collapse. However, this method will require more power than contour welding. Simultaneous welding will have the same effect and will result in a more uniform compression of the material across the entire weld zone.
Part design is important and attention to welding should be assessed during the part is design. The material of construction should be evaluated. If dissimilar parts are to be joined they should be chemically miscible and also should have similar melting temperatures. Chemically resistant materials such as PEEK, Polysulfone, and fluorocarbons are being used more widely. However, these materials are difficult to weld. A scanning system would be more effective when working with this type of material. The use of fillers such as fiber glass will adversely effect the welding of plastics since they will diffuse the laser energy. The thickness of parts also is something that should be considered. Thin films tend to overheat and require special attention. Thicker semi-crystalline plastic parts also will diffuse the laser energy. A guideline for the thickness of semi-crystalline parts would be between 1 and 5mm. The mating of parts is something that should be considered. For contour welding, gaps should be less than 100 microns. And rough surfaces can result in poor surface-to-surface contact and weaker welds. Finally warping of parts prior to welding can cause gaps in the weld joint.
Overheating of parts and cooling of parts should be understood. Overheating of parts can cause warping or entrapped bubbles during welding. The use of heat sinks and cooling plates under parts can be valuable. A heat sink is a metallic plate that can be used to absorb heat from the welded parts. This will prevent melt-through or overheating of the lower surface of the part. Rapid cooling of the lower part also will be of benefit. We have found that this will reduce warping of thin parts and improve the appearance of some welds.
Understanding of the laser welding process is an important factor in development of this joining technique. The lack of attention to part design can lead to poor joints and high tooling costs. The proper mating of parts is very important. The selection of the optimum optical system to fit the part is an obvious factor. And attention to molding also is a key factor. The end user should work with the molder and optimize the weld areas in order to reduce non-uniformities and part warping in those areas.
Smaller Line Widths
A major effort is being made to reduce the size of laser weld lines. This effort is being driven by the demands of the microfluidics market. Microfluidic devices handle small volumes of fluids, generally in the microliter and nanoliters ranges, and are used for analysis in chemical, environmental and medical applications. Earlier devices have been referred to as lab-on-a-chip devices. As illustrated in Figure 5, the devices are also small, usually several milliliters in length and width. Within these devices, fluids flow through small capillaries of less than 1mm in diameter or width. The size of the channels results in laminar flow of fluids and capillary action that enhances the chemistry of the devices. They can therefore be used to perform many standard chemical separations, reactions and analyses, but with a minimum amount of fluid.
One of the problems associated with the devices is the assembly of two or more layers of plastic to form the chips. In these devices integrate arrays of channels must be hermetically sealed without altering the surface properties of the channels. Standard joining techniques such as adhesives and ultrasonic welding result can result in the blockage of the very small channels that carry the fluids. Laser welding has been shown to be a good method of joining microfluidic devices. However, the microfluidic developers have demanded smaller weld joints.
The field of microfluidics has increased activity in micro manufacturing. The initial work was derived from MEMS technology using silicon substrates. However commercialization efforts have led to the development of plastics as replacement for costly silicon or glass substrates. Companies such as Precision Microfab (Severna Park, MD) have developed micro machining, marking, and welding techniques that deal with the problems of miniaturization of parts.
Chin, Zybko and Clements of Leister Technologies have investigated the use of diode lasers to weld microfluidic devices with channels of 100 microns that were formed by injection molding of parts2. They used 80 watt to 120 watt diode lasers to produce weld lines with a minimum weld size of 100 microns. A key to their success was the use of a masking system to protect the channel integrity. The positioning of the mask was critical to the welding operation. They were able to optimize the melt flow by using computer assisted positioning of the mask. They indicated that melt flow depended strongly on the viscosity of the plastic and the welding velocity.
Li et al of the Fraunhofer Institute used a scanning laser system for rapid processing of microfluidic devices3.
Fargas et al. of Laser Zentrum Hannover used a 940nm laser with a Globo head to weld PET film to a microfluidic device4. The film was coated with Clearweld absorber and welded at 30 watts and speeds of 700 to 1000 mm/sec.
Grewell and Benatar of The Ohio State University produced 50 micron weld widths on clear to carbon filled polycarbonate5.
Jones of TWI, Ltd studied Nd:YAG, diode and fiber laser sources using coatings, absorber-in-resin and thin films between parts6. The minimum welds achieved were similar to the focused beam width when absorbers were incorporated into one of the parts. With films, the film needs to be melted in addition to the substrate parts and the width of the weld increased by at least as much as the thickness of the film. Narrower lines were achieved when the absorber was added to the resin rather than when used as a coating or a film.
Boglea and Gillner of Fraunhofer-Institut fur Lasertechnik ILT achieved micro welding of plastics using a 9W fiber laser (1112nm) with a 30 micron beam using a rapid circular motion along the direction of feed of the part7. The width of the weld seam was less than 500 microns. They reported the welding of PMMA and PC at laser outputs of 3.5 watts and speeds of 2 m/min.
Ussing et al cited difficulty in welding microfluidic channels in 20 to 100 micron range because even small amounts of stray melt might fill a part of a channel8. They used a commercially available diode laser (0.2 to 0.5 watts) with a 50 X 5 micron beam size to achieve weld seams of less than 10 microns at a welding speed of 15mm/sec with no noticeable spread of the weld.
A series of studies have been conducted by Haberstroh, Hoffmann, et al of the Institute of Plastics Processing (IKV, Aachen, Germany)9-11. Their work has covered a wide variety of factors such as carbon content, the use of organic absorbers and thin films between layers.
Market Trends
What are the areas of growth for laser welding of plastics? Laser welding will continue to grow in traditional areas, such as automotive and electronic applications. However, the biggest growth should occur in the field of medical devices. The area of microfluidics has already been discussed in brief detail. The volume of parts that will be made in order to conduct chemical analysis on a micro scale is staggering. A second welding application that will expand quickly is the area of medical tubing. Every time a medical tube is used, it must be joined to a fitting, a fixture, or a medical bag of some sort. Work by B. Donohue of Natvar (Clayton, NC) has led to the development of a laser welding system for medical tubing (Figure 6). It has demonstrated the versatility of this system using a contour, diode laser designed and built by Branson. In addition to tubing with infrared absorbers blended into the resin, Natvar produces co-extruded tubing that facilitates the welding of two and three layers of tubing to medical connectors by placing the absorbers only in the outermost layer of the tubing.
Another area of growth for laser welding is in the construction of fuel cells. Several projects are currently using laser welding to join multiple layers that constitute fuel cells. Generally, these cells are designed to replace batteries on smaller electronic devices. The size of the cells is therefore small and requires accurate placement of the weld joints. At the other extreme, the cells may be quite large. However their complex shape and use of chemically resistant plastics makes other joining techniques non-viable. There has been work in fuel cell development by Barkston Plastics, Ltd (Leeds, UK), Gentex Corporation, and Leister Technologies.
The electronics industry seems to be a natural target for laser welding. The elimination of vibration, as encountered in ultrasonic welding, has provided a satisfactory way to join plastics containing delicate electronic components such as miniature printed circuit boards. Since most electrical enclosures can be constructed with black substrates it is an ideal market for carbon black welding. Devices requiring other colors must rely on infrared absorber systems. An example of this would be the cell phone market. VTT, a Finnish research facility, has done extensive work on laser welding of cell phones.
Other areas of growth for laser welding processes are thin films, solar cells, and thermal plastic elastomers. The welding of thin films has been a problem because of overheating of the film. The films tend to be destroyed before a rigid part to which it is being welded reaches it melt temperature. The use of scanning techniques has shown promise in this application. Solar cells are traditionally made of quartz or silicon. However, there have been significant advances in the use of plastic for solar cell applications. These cells are currently operating at an efficiency of about 5 percent as compared to the approximately 15 percent efficiency of quartz cells. It is felt that laser welding will be a viable method of joining solar cells in the near future. Another area of growth for laser welding is in the field of thermal plastic elastomers. Research efforts have been undertaken by Allod (Germany) and GLS (US) into the use of laser welding of these materials.
Laser welding of plastics is a clean, non-contact process that does not generate fumes as in solvent bonding and hot plate welding. Vibration of parts as in ultrasonic welding is not a factor. It doesn’t require the use of additional materials as in adhesive bonding. Laser welding doesn’t change the chemical or physical properties of the plastics. And the environmental issues associated with solvent and adhesive bonding are eliminated.
Laser welding will not displace other types of welding processes. It doesn’t make sense to invest in a laser system if a less expensive system such as ultrasonic welding works. There must be a need that can justify the cost of the system. The fields of electronics and medical devices are therefore attractive targets for laser welding of plastics.
References
- D. Smock, Design News, April 9, 2007,
- J. Chin, J. Zybko, and J. Clements, Nanotech, 2, 483 (2005)
- B. Li, T. Schwartz and A. Sharon, Journal of Micromechanics and Microengineering, Nov (2006).
- M. Fargas, D. Herzog, O. Meier, H. Haindl and F. Tolkmitt, International Medical Devices Conference and Exposition, 2007, 29 (2007)
- D. Grewell and A. Benatar, A, Proc. ANTEC Conference of the Society of Plastic Engineers, May, 1039 (2003)
- I. Jones, Precision Laser Welding of Plastics, TWI, 2007
- L. Boglea et al., Microsystems Technologies, 10, 187 (2004)
- T. Ussing, L. Petersen, C. Nielsen, B. Helbo and L. Hoislet, The International Journal of Advanced Manufacturing Technology, 33, 198 (2007)
- E. Haberstroh and W-M Hoffmann, Society for Optical Engineering (SPIE), Proceedings of Photonics West Conference, San Jose (CA), USA, 2007
- E. Haberstroh, W-M Hoffmann, et al. Proceedings of Conference on Multi-Material Micro Manufacturing, Oct (2007)
- E. Haberstroh and W-M Hoffmann, Journal of Engineering Manufacture, 222, 47 (2008)
Bill Cawley is a process chemist with over 35 years of experience in coating systems and is currently responsible for Clearweld coatings that are used in the laser welding of thermoplastic materials. Gentex Corporation is a manufacturer of integrated life support and protective systems that are used internationally by military, homeland security, and civilian organizations. It operates production facilities in five locations in the United States. For more information about Clearweld or Gentex Corporation visit www.gentexcorp.com.