Best Practices for Bonding Semi-Crystalline Thermoplastics
by Scott Sabreen
The Sabreen Group
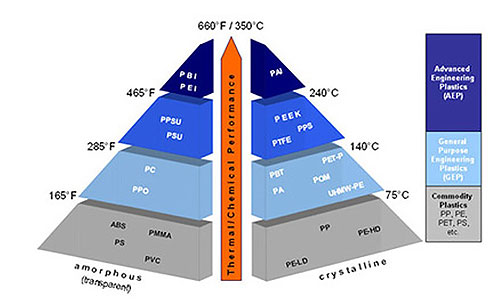
Illustration 1. Examples of semi-crystalline polymers include acetals, nylons, polyolefins, PEEK, PPS and LCP.
From commodity to high-performance grades, semi-crystalline polymers are difficult to bond to themselves and dissimilar materials. To create strong molecular bonds necessary for adhesion, clean substrate surfaces (often in conjunction with pretreatment) are required. The selection of adhesive and proper curing are critical to achieving the desired end result.
Generally, polymers exhibit two types of morphology in the solid state – "amorphous" and "semi-crystalline." Under certain conditions, some polymers can exhibit both morphologies. In amorphous polymers, e.g., acrylic and polycarbonate, there is no true melting point (softens gradually). The molecules are oriented randomly and are intertwined (like cooked spaghetti), with a glass-like transparent appearance. In semi-crystalline polymers, there is a sharp melting point and the molecules pack together in ordered regions having regular linear structure. Since crystallites scatter light, they typically are more opaque. Semi-crystalline polymers tend to form tough plastics because of the strong intermolecular forces associated with close chain packing. (See Illustration 2.)
Semi-crystalline polymers inherently are difficult to bond because they are hydrophobic, chemically inert and possess poor surface wettability (i.e., low surface energy). While these characteristics are highly desirable for performance, poor surface wettability creates bonding challenges for manufacturers. Further, semi-crystalline polymers, such as nylon, absorb moisture in excess of three percent of its mass of water from the atmosphere. Moisture, in and of itself, creates adhesion problems. Therefore, it is important to perform bonding processes as soon as possible following molding operations or package the parts tightly in non-poly bags with a desiccant. Proper drying procedure is critical to processing and part performance.
Surface cleaning and pretreatment
Surface preparation is critical to achieving high adhesive bond strength. Surfaces must be clean and contamination-free from dirt, grease and oils. Low molecular weight materials (LMWM) such as silicones, mold release products and anti-slip agents inhibit bonding. To suitably clean semi-crystalline surfaces and remove LMWM materials, moderate to higher strength Toluene, Xylene, Acetone or MEK (in accordance with company solvent policy and state law) generally should be used. Polymer data sheets will reference suitable cleaning agents. Alcohol is a weak solvent and only removes superficial dirt, but not hydrocarbon contaminates.
Proper technique must be used at all times, including the use of lint-free cloths and wearing powder-free protective gloves. Excess solvent creates weak boundary layers of un-removed chemicals, leaving a haze build-up that will inhibit bonding.
Semi-crystalline polymers bonding applications often require plasma pretreatment immediately following solvent cleaning. Gas-phase surface oxidation pretreatments include electrical corona discharge, electrical atmospheric plasma, electrical air plasma, flame plasma and low pressure RF cold gas. These processes are characterized by their ability to generate "gas plasma," an extremely reactive gas consisting of free electrons, positive ions and other species. Chemical surface functionalization also occurs. In the science of physics, the mechanisms in which these plasmas are generated are different, but their effects on surface wettability are similar. Each method is application-specific and possesses advantages and/or limitations.
For example, electrical pretreatments do not remove/clean all poly-aromatic hydrocarbons, so it may be necessary to continue solvent cleaning. RF Cold Gas pretreatment will remove hydrocarbons, thus pre-cleaning is not necessary.
As a general rule, acceptable bonding adhesion is achieved when the surface energy of the substrate is approximately 10 dynes/cm greater than the surface tension of the liquid or adhesive. The surface energy of untreated nylon is approximately 40 dynes/cm. Therefore, the desired post-treatment surface energy needs to be in the range of 50-54 dynes. In this situation, the liquid is said to "wet out" or adhere to the surface. A common method for measuring surface energy "wetting" is the use of calibrated dyne solutions in accordance with test method ASTM D2578.
Adhesives and curing
By definition, "adhesion failure" occurs at the interface between the adhesive and the adherend (substrate). Visually, there is residual adhesive remaining at any location on only one surface and not the second substrate adherend. Optimal joint design is critical in any adhesive bonding application. Bonded joints can be subject to tensile, compressive, shear, peel or cleavage forces, often in combination.
For many semi-crystalline polymer adhesive bonding applications, structural adhesives (including epoxies, acrylics and urethanes) are commonly utilized. Two-component epoxy consists of mixing an epoxy resin plus a hardener or procuring "duo-pak" applicators. Uniform, thin bond line thickness (0.002 to 0.007 inches) is preferred for optimal shear and tensile strength properties. Full cure time typically is in the range of seven days at 75°F, but is variable between applications and environment conditions. The speed of cure can be accelerated by adding heat (120-210°F) which results in additional polymerization and can give the epoxy better properties. The polymer’s Heat Deflection Temperature generally is the upper limit for post-molding processing applied heat. Bake time and temperature is application-specific.
A common mispractice is to apply extra adhesive to improve bond strength. Excessive adhesive is detrimental and a leading cause of bonding failures. For example, epoxy adhesives have relatively high coefficients of thermal expansion. Bond lines need to be kept thin and uniform in thickness (typically 3-5mil for maximum shear strength). The adhesive supplier can provide guidance for optimal bond line thickness for the specific application. Pre-measured "duo-pak" applicators will eliminate mixing problems and provide a more exact mix ratio. They also provide better stoichiometric chemical reactions, resulting in better strength and outgassing properties.
Relative to the surface texture of the part to be bonded, as molded, a textured surface will increase mechanical interlocking adhesion in addition to solvent cleaning and plasma pretreatment. Texture can be accomplished within the mold tool or manually using a Scotch-Brite pad. For example, NTMA mold cavity Finish "40-Diamond buffed 1200 Grit" likely will improve bond strength versus Finish "10-Fine Diamond 8000 Grit" (0-3 micron range). Even slightly textured surfaces will be beneficial. (See Illustration 3.)
In summary, to achieve high-strength adhesion bonding of semi-crystalline polymers, the following are recommended:
- Ensure the resin is properly dried before molding.
- Conduct the bonding process as soon as possible following molding.
- Clean the part surface with solvent to remove surface debris and hydrocarbon contaminates.
- Consider implementing a plasma surface pretreatment to increase surface wetting/chemical functionalization (in addition to solvent cleaning).
- Apply a thin, uniform adhesive bond line. Additional benefits can be gained if the product has a textured surface.