Understanding Reactive Gas Technology
Reactive Gas Technology Offers Performance and Design Flexibility
by Prakash Iyer
Inhance Technologies
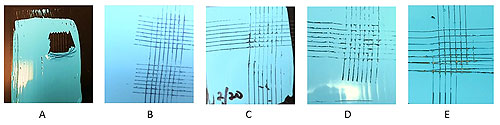
Figure 2: Results of a crosshatch test on TPO (ADX 1310) after treatment and painting: A) Untreated TPO, B) Treated and stored for one week, C) Treated and stored for two weeks. D) Treated and stored for four weeks and E) Treated and stored for 10 weeks, prior to painting. Low VOC architectural paint was used for testing.
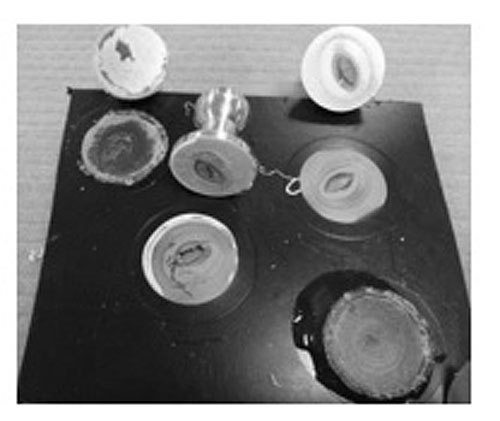
Figure 3: Image showing cohesive failure of the substrate when tested with epoxy (clear) and urethane (white adhesive) on RGT treated TPO plaque.
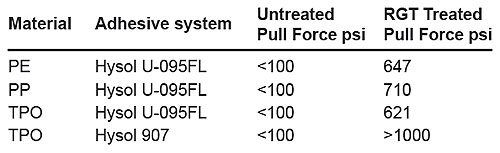
Table 2: Defelsko test pull forces required to delaminate metal pawns from RGT treated polyolefin surfaces.
Commodity polymers, such as polyethylene and polypropylene, often are chosen over engineering or high-performance polymers due to factors that include lower costs, availability and broad processing latitude. These materials, however, often exhibit very low surface energy, which creates poor adhesion characteristics and leads to poor printability, adhesive assembly, composite production or metallization. There are a number of techniques to overcome these drawbacks through the application of various forms of energy to temporarily activate the surface for subsequent processing, including flame, plasma and corona treatment. Another effective means to activate surfaces is the use of reactive gases to impart permanent increase in surface energy. This article discusses the fundamental features and industrial applications of gaseous surface activation of polymers using Inhance Technologies’ Reactive Gas Technology™ (RGT).
Understanding RGT
Surface activation of hard-to-bond polymeric surfaces generally is accomplished by imparting polar functional groups that "activate" the surface. RGT, or fluoro-oxidation, of polymers describes the heterogeneous reaction of gaseous fluorine and oxygen with a polymer surface. This method results in modification of only the surface of the polymer, to a depth of 0.01 microns to 10 microns, not affecting the materials’ bulk properties. The activation of the surface occurs rapidly upon exposure to the reactive gas mixture (exposure times can be as low as fractions of a second) and can be carried out in a batch process or continuous process. The process is carried out under controlled pressures, which provides the ability to tailor the degree of functionalization, as well as ensures isotropic distribution of the treatment. The result is extremely uniform treatment of all surfaces of a two- or three-dimensional product, including all sides, deep reliefs, curves and edges. Alternatively, selective surface functionalization can be obtained through orientation, masking or partitioning techniques. Since a large number of items can be treated at a single time or continuously, the production rates can be targeted to match virtually any manufacturing scenario. Materials that can be activated using RGT include polyethylene, polypropylene, thermoplastic polyolefins, thermoplastic elastomers, thermoplastic vulcanates, polycarbonates, acrylonitrile-butadiene-styrene, acrylonitrile-styrene-acrylate, polyesters and numerous other polymers.
RGT utilizes a mixture of reactive gases, including elemental fluorine and oxygen, to activate polymeric surfaces. Fluorine quickly activates the polymer surface, generating free radicals, which promotes the reaction of oxygen to create a functionalized surface. The process can be controlled to incorporate very slight to very high functionalization. RGT integrates fluorine and oxygen moieties to a polymer containing extractable hydrogens, shown in Figure 1, increasing the polarity of the surface. The resulting functionalized polymer exhibits high surface energies, which can be utilized in downstream processes including adhesive assembly, coating, printing and metallization. RGT primarily works to increase the polar component of surface energy, which results in higher and more durable bonding performance.
RGT results in permanent modification of the surface, not only through the development of covalent functional group incorporation, but also by locking the functionalities created on the surface in place by light crosslinking. Treated materials, including continuous webs as well as discrete parts, maintain high surface energies for months and years, even following exposure to extreme environments, such as water and solvent washes, detergents, elevated temperatures and weather.
The extent of treatment using RGT can be verified using a number of readily available analytical techniques, such as X-ray Photoelectron Spectroscopy (XPS), Fourier Transform Infrared Spectroscopy (FTIR), Contact Angle measurements, Surface Energy measurements or Scanning Electron Microscopy (SEM). Estimation of surface energy by the use of dyne pens or dyne liquids is the most common method to quickly measure the surface energy of treated plastics.
Applications of reactive gas technology
RGT surface modification is applicable to a wide variety of materials and currently is utilized in numerous manufacturing settings. Table 1 lists common plastics that are commercially treated to increase surface energy for numerous applications. Materials that cannot easily be activated using other technologies, such as polysiloxanes and polyacetals, can be activated by RGT even under room temperature conditions in a continuous fashion.
Thermoplastic polyolefins (TPOs) are used widely in the automotive industry, due to their broad range of tunable properties. Many TPO grades are high in rubber content (and higher in cost), in part to allow for solvent-based primers to activate surfaces for decoration. However, numerous grades contain lower rubber content, making solvent-based primers ineffective. RGT permanently activates both low and high rubber content TPO panels for painting, adhesive bonding or printing. Crosshatch paint testing (ASTM D3359) indicated perfect 5B results, even after 10 weeks of storage of the TPO plaques (ADX 1310) after treatment, followed by painting. Figure 2 shows the crosshatch test results, wherein samples were stored for different periods prior to painting.
PE, PP and TPO panels treated using RGT allow for adhesive bonding of polyolefins using traditional urethane- or epoxy-based adhesive systems without any special surface preparation. To demonstrate, two different adhesives – Loctite Hysol U-095FL (urethane) and Loctite Hysol 907 (epoxy) adhesives – were used to glue a metal pawn on activated PE, PP and TPO surfaces. After 24 hours of cure of the adhesive, a Defelsko tester (ASTM D4541) was used to test the force required to delaminate the metal pawn from the TPO surface. Results showed that there was a sevenfold increase in the pull strength required to separate the pawn from the TPO surface, and each time the mechanism of failure was cohesive failure of the substrate. Figure 3 depicts the visual results from the test, while Table 2 shows the numerical data.
RGT also can be used to improve the efficacy of water-based adhesives, which are gaining traction due to their reduced ecological impact and associated costs. These adhesives, however, do not usually perform favorably with polyolefins. By activating the surface using RGT, the adhesives wet out the plastic surface evenly without blistering and peel off, resulting in excellent adhesion long after treatment. Figure 4 compares the effect of applying a water-based adhesive (3M ‘77’ low VOC adhesive) on an untreated TPO surface and a RGT-treated TPO surface. In case of the untreated TPO surface (Figure 4A), it is evident that the adhesive fails to wet the surface of the TPO (blistering of the adhesive), as well as complete delamination of the adhesive (lack of bonding). In contrast, RGT-treated TPO plaque (Figure 4B) shows uniform wet out of the surface without blistering, as well as perfect crosshatch test results.
The use of urethane foams to create soft-touch surfaces in automotive interiors is common. Often, the rigid substrate for center consoles and dashboards is polyolefin-based, often TPO. RGT treatment of these substrates eliminates the need for any tie-coats, primers or boundary layers, allowing bonding strengths that exceed the cohesive strength of the foams used to achieve the soft-touch feel.
The use of chlorinated polyolefins (CPO) in the automotive industry to improve adhesion of paint on the exterior plastic parts of vehicles is the predominant mechanism of surface activation for such parts in North America. This practice is being challenged due to the nature of the solvents utilized. In Europe, CPO primers have been replaced with alternate technologies for improving paint adhesion, including flame treatment, plasma, corona and RGT. RGT enables TPOs to be painted directly with excellent paint adhesion results often performing at least 50 percent better than solvent-based CPO primers.
Additionally, RGT provides the ability to quickly treat complex parts thoroughly, without complex robotics or fixtures. Table 3 shows the comparison of CPO primer and RGT-treated TPO plaques evaluated against several GM specifications. RGT-treated TPO plaques pass all the test specifications for automotive bumpers and also exhibit 50-percent less delamination of the paint as compared to CPO-primed bumpers, which can reduce paint scratches and peeling for the life of the vehicle.
RGT is a very versatile process, allowing all forms and shapes to be treated. The options to customize the treatment conditions and the equipment to suit customer specifications are infinite. From large batch processes to continuous, inline operations, RGT provides significant flexibility in manufacturing design and operation for an unlimited variety of shapes and sizes, including three-dimensional articles, films, continuous fibers, plastic pellets and resin powders.