Durable Graphics Add to Product Security, Branding
Solutions Available for Both In-Mold and Post-Mold Decorating
Plastics Decorating
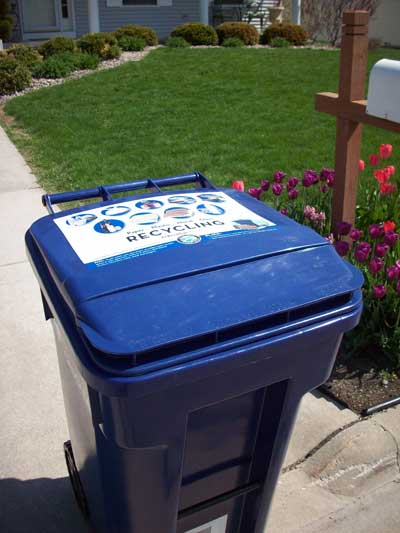
Common applications for in-mold labels are in the appliance, automotive and lawn and garden markets for products such as medical waste containers, recycling and waste curbside containers and outdoor furniture.
For long-term branding and identification in difficult conditions, durable graphics have a step up on their pressure-sensitive labeling counterparts. For markets in which safety information or parts identification are crucial, the ability to fuse the label directly to the plastic part has answered a need for labeling that can withstand extreme conditions or deliberate attempts at removal.
In-mold labeling is accomplished during the injection molding or blow molding process, fusing a printed label to a molded part. This process creates a win/win scenario for those wanting the visual impact afforded by screen or pad printing, while still delivering a long-lasting graphic that does not require secondary processing. For those without the ability to apply labeling during the molding process, new technology now allows post-mold fusing of a label to plastic parts, creating another option for those desiring the permanence and longevity of durable graphics.
In-mold labeling avoids secondary decorating process, reduces waste
Labels applied as a part of the molding process are fused permanently to the resin, avoiding the undesirable profile of a raised label and eliminating the chances of the label peeling off or elements such as dirt or water getting between the label and the product, loosening its hold. In addition, according to Becky Murphy, marketing manager for Romo Durable Graphics, durable graphics provide the added benefit of reducing the labor and material costs associated with secondary applications, hot stamping, heat transfer and pad printing. "In-mold labeling provides a result that looks like a high-quality pad printed label without the high-quantity scrap," she explained. Labels applied during the molding process also meet standards established for chemical, UV and weather resistance.
According to Butch Kaplan, general manager of Central Decal, in-mold labels have distinct advantages, particularly when considering product liability issues. "The beauty of an in-mold label over a pressure-sensitive label is that the label becomes part of the plastic," he explained. "To get the in-mold label off the product, you would need to destroy the plastic."
Common applications for in-mold labels are in the appliance, automotive and lawn and garden markets for products such as medical waste containers, recycling and waste curbside containers and outdoor furniture. In-mold labeling also is used in consumer packaging (detergent, shampoo, butter, etc.) and consumer goods like phones, automotive decoration and toys.
The in-mold labeling arena continues to evolve, with new applications and decorating options entering the arena. Central Decal has focused on low-cost, low-volume durable goods that require customized labels that may be more extensively decorated than typical durable labels. "With our latest technology, we have created a hybrid process that combines a variety of printing processes into one: flexo, digital and screen," said Kaplan. "Combining these processes allows us to print durable variable data and high resolution pictures without sacrificing outdoor durability."
Romo Durable Graphics, which designs in-mold material, inks and coatings, has focused on improving the durability and ease of use of in-mold labels. "We offer glossy and slip-resistant surfaces and can print up to 4x6' size," said Murphy. "Durability options include outdoor UV, scratch, solvent and high-heat dishwasher resistance."
iMIG technology allows post-mold permanence
MIGS®, a manufacturer of permanent graphics and enhancement products for PE/PP products in the rotational molding industry, has created a new division: iMIG®. The iMIG technology is a post-mold process that utilizes a company’s existing hot stamp or heat transfer equipment to apply a fully compatible finished graphic to polyethylene and polypropylene products.
Jason Brownell, vice president of sales for iMIG, explained, "If a decorator or molder already owns hot stamping or heat transfer equipment, no new capital expenditures are required to apply a more permanent labeling option. The company’s bottom line reflects that benefit."
iMIG relies on three variables: heat, time and pressure. The iMIG graphic is applied by melting two like materials together. This requires a higher die temperature than typically seen with hot stamping or heat transfers, approximately 450º F (232º C). This added heat causes the graphic material to reach its melt temperature, fusing it to the skin of the PE/PP product. Dwell time is dependent on the melt flow characteristics of the PE/PP being decorated, but typically is between .5 to 2 seconds.
The iMIG graphic application process only requires 175psi. Compare this to foil stamps, which need approximately 400psi, and heat transfers (around 450psi). The lower required pressure means larger images can be fused with a smaller tonnage machine. Large iMIG labels (such as 8x10") can be applied to the product with a vertical hot stamp/heat transfer machine. Heat transfers of a similar size would need to be rolled onto the surface with a roller-style machine.
Because the iMIG graphic and the PE/PP product become one during the application process, the iMIG graphic has the same characteristics as the base material. The graphic has consistently passed chemical- and weather-resistance tests, while also consistently scoring a 5A (the highest possible score) in the ASTM D3359-09 test method covering procedures for assessing the adhesion of coating films to substrate.
This post-mold method of applying durable graphics is not limited to logos and warnings. With iMIG technology and the use of LaserCode, manufacturers can achieve a durable method to capture serialized numbers and bar code tracking information. Browning explained, "iMIG graphics utilize laser-reactive pigments that change from white to charcoal-grey when exposed to specialized lasers. This system can be used on the pre-applied graphic or directly to the graphic after being fused onto a product."