Q&A: Laser Welding of Plastics
by John Paul "J.P." Kurpiewski
Branson Ultrasonics Corporation
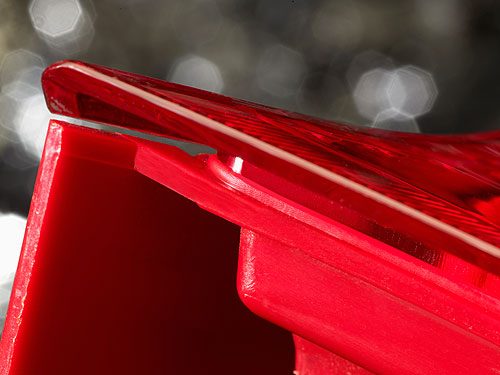
Plastic welding is a process in which heat is generated to melt plastic and form chemical bonds upon re-solidifying.
What is a laser?
In nature, light exists across a spectrum of wavelengths, ranging from very short (X-rays and gamma rays) to very long (radio waves). Humans only can see visible or "white light" of wavelengths from around 430-690 nanometers (nm).1 A laser beam is an amplified concentration of light energy at a specific wavelength. It is coherent light, which allows focusing on a tight spot and a narrow beam over long distances. The word LASER is an acronym, which stands for Light Amplification by Stimulated Emission of Radiation.
What is laser welding of plastics?
When light reaches a material, it can be transmitted, reflected or absorbed. Some materials, such as glass and water, allow white light to be transmitted. Mirrors and smooth surfaces reflect. Some solids, such as road pavement or black car seats, absorb the energy and convert it to heat.
In general, plastic welding is a process where heat is generated to melt plastic and form chemical bonds upon re-solidifying. Other welding processes, such as ultrasonic or vibration, generate heat from friction caused when parts impact or are rubbed together. However, laser welding can create heat without contact or harsh forces, thus resulting in a more precise, aesthetically cleaner weld.
Laser welding requires two parts: one which is transparent to laser and the second which absorbs. Figure 1 demonstrates how the laser beam can be directed through the transparent part to where it hits the absorptive material and gets converted to heat. This is known as Simultaneous Through Transmission Infrared (STTIR) welding. The two parts must be in good contact and held together with force. Then, the heat generated can conduct across the interface of the two materials to melt them both. When the laser is turned off, the parts cool and are bonded as the weld solidifies.
What materials work best using laser?
Years of research by the materials and welding industries have shown that various plastics have different absorption characteristics. The amount of laser energy absorbed can depend on material composition, thickness, molecular structure, chemical additives and wavelength applied.
In laser welding, transmissive and absorptive parts are needed. This could be accomplished with two different plastics, such as ABS and PMMA. It also can be achieved with two similar materials by adding laser-absorptive dyes to one part. Amorphous plastics tend to be more transmissive than semi-crystalline. In semicrystalline plastic, crystal interfaces cause internal reflection and more energy dissipation.
Wavelengths around 1,000nm, referred to as "near-infrared," are demonstrated to be optimal in transmission and absorption across a wide range of materials. As wavelengths approach 2,000nm, most plastics absorb the energy and both mating parts can heat up throughout, which can limit this technology to thinner parts.
It is noteworthy that although parts may be transparent or opaque to visible white light, they may behave differently to near-infrared light. For example, a part may appear opaque to the eye, which is sensitive to approximately 430-690nm. However, the part might not absorb near-infrared laser energy around 1,000nm and be an excellent transmissive layer.
Interestingly, laser technology even has been used to weld thermoplastics to thermosets. Thermoset plastics typically do not melt when reheated, making them difficult to weld. Through experimentation, Branson found that laser can succeed when other welding technologies struggle.
There are a myriad of plastics and combinations known to be compatible with laser welding. The forefront of material science continues to move forward, and new plastic combinations and additives regularly are being discovered. The possibilities are numerous and growing.
What are the benefits of laser welding?
First, the weld quality is outstanding. Laser welding is a precision process, with typical weld depths around 0.2mm, compared with 1.5mm for vibration welding. Branson has achieved weld depths of 0.05mm with its products, and weld widths of 0.001-0.005mm were achieved recently at an external research institute.2
The resulting appearance of the weld is superior to other technologies. Less excess material is generated. No particulates or "flash" are created in this clean process. This is of particular interest in medical applications and filtration devices.
Weld strength varies by material combination, joint geometry and application. However, along with its material suppliers and customers, Branson has seen evidence that some laser welded parts have stronger bonds than traditional joining techniques. Seals can be made hermetic.
Three-dimensional part geometries can be welded with laser beams positioned on many axes. In comparison, vibration welding requires a weld plane and only allows a limited angle of deviation. With laser welding, engineers and stylists have much more design freedom to shape a product.
Laser welding has the advantage of accommodating sensitive parts. Because there is no vibration, friction or harsh lateral forces, delicate plastics or assemblies with embedded electronics can be welded. The simultaneous laser weld process offers excellent speed of production and short cycle times. Branson’s patented weld process demonstrates weld times of approximately 0.5-5.0 seconds.
The simultaneous laser weld process also accommodates the same part tolerances as alternative technologies, keeping tooling costs low. Controlled precise melt collapse is achieved.
Are there any application challenges or situations where laser would not be the best approach?
The laser welding process requires two parts with different absorption characteristics. Not all polymers are transparent. The parts also need to be firmly pressed together to enable heat conduction across the interface. The geometry of the joint also must be considered and be accessible to laser energy
.What are popular laser applications used in today’s market segments?
Laser welding use is growing in several important market segments. Due to the significant advantages of laser welding, Branson is seeing more use in medical, automotive, consumer electronics and home personal products applications. Medical applications include wearable drug delivery systems, filtration and microfluidics. Automotive components include sensor housings, filter assemblies, instrument clusters, tail lamps, irrigation systems and fluid reservoirs. Consumer electronics include ink jet printer cartridges and audio speakers. Home personal products include food dispensers and more.
Where do you see the future of this technology?
The evolving and ever-changing plastics industry continues to raise the standard for the aesthetics and performance of plastic weld joints. The numerous benefits of clean, particle-free, superior welds in a non-contact, vibration-free assembly method make laser technology ideal for today’s applications and the challenges of the future.
References
- Halliday, Resnick, and Walker. Fundamentals of Physics. 5th ed., Vol. 2. New York: John Wiley & Sons, Inc. 1997.
- Sweeny, Kate. "TWI and Cambridge University Create World Welding First." TWI and Cambridge University Create World Welding First. Business Weekly, 5 June 2015. Web. 30 June 2015.