Laser Texturing Adds Another Level of In-Mold Decoration Possibilities
by Chad Hase
GF Machining Solutions
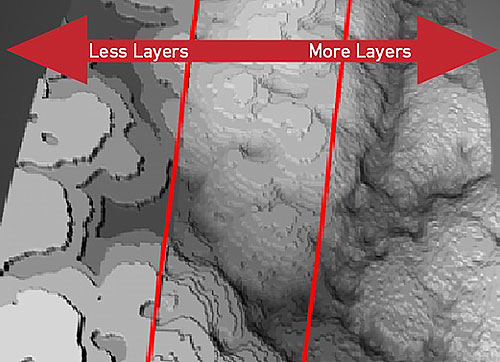
Image 1. When more layers are added, the texture becomes smoother and more realistic.
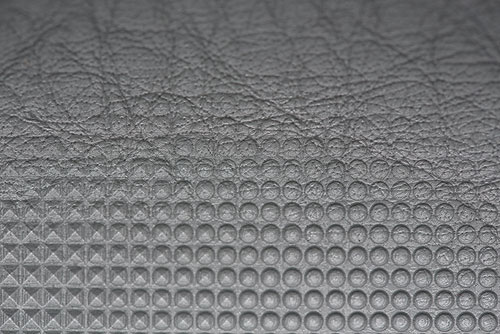
Image 2 shows a leather texture being blended into a dimple texture via laser texturing.
Laser texturing allows for intricate and consistent designs to be added to injection molds for decorative purposes. These textures enable individualization of products ranging from automotive components to packaging by mimicking the look of leather, wood, geometric patterns and much more. When compared to conventional surface treatment using chemical etching processes, laser texturing can offer ecological and design advantages.
What is laser texturing?
Deriving their name from an acronym for Light Amplification by Stimulated Emission of Radiation, lasers are electronic optical devices that generate a very intense and narrow beam of monochromatic light by amplifying photons with more energy through collisions with other photons. While the technology has existed for over half a century, applying it to the generation of textures on materials is a relatively recent development.
Programming for laser texturing begins with saving a texture as an 8-/16-bit grayscale tiff or JPEG. One thing to remember with this process is that the darker the black, the deeper the ablation. The opposite also is true, meaning that the closer to white, less the ablation that is taking place.
The advantage of working in the 8-/16-bit grayscale environment is that it provides the user over 65,000 layers in which to work. On the other hand, traditional chemical processes limit users to working with 5-10 layers. With each additional layer added to a final product, the final texture becomes smoother and more defined (see Image 1).
What is the advantage to laser texturing vs. chemical etching?
Laser blasting/laser texturing is a completely digital process. This provides manufacturers with confidence in consistency, as the part will have the same finish whether it is manufactured in the US, China, Europe or another part of the world.
A fully digital process also enables the creation of new textures that were not previously possible because of the limitations of chemical etching. Image 2 demonstrates how a completely digital process provides the opportunity to seamlessly blend different textures into one. This example shows a leather texture being blended into a dimple texture, all on a single workpiece.
Are there times when chemical etching still makes sense?
Going fully digital to avoid etching provides substantial advantages, such as reducing the need for harsh chemicals and reducing turnaround times. However, there still are times when chemical etching makes sense. Some textures have been patented with the chemical etching process and, until the patent has expired, the process cannot be altered. There also are some situations where extreme roughness/hardness is required. In those cases, chemical etching is the better choice.
Many manufacturers are starting to adopt a hybrid approach. In most of these cases, a manufacturer will remove the masking with the laser before moving the workpiece to the chemical processor. Especially in cases of highly complex molds, the 5-axis laser system helps to ensure that textures are maintained with perfect control as they go over edges or welding lines.
How is laser blasting different from laser texturing?
Similar in concept to sand or glass blasting, laser blasting is a process for texturing or cleaning a surface. The advantage of laser blasting over sand or glass blasting is the repeatability. With laser blasting, the same finish is achieved every time. Furthermore, manufacturers can ensure that they get the specific surface finish that they want. Laser blasting also offers the ability to remove milling marks and burrs to ensure a completely smooth surface.
What are the advantages of the laser texturing process?
Transparent design process: Laser texturing files can be created from scratch in-house or include surfaces derived from natural sources via reverse engineering with a 3D scanner (see Image 3). The CAD/CAM software for the laser process allows transition-free patching, UV mapping for applying texture and 3D simulation, resulting in a ‘‘what you see is what you get’’ situation for the programmers.
Consistent quality: Laser ablation also allows a user to maintain a smooth and flawless texture across parting lines in a mold. If there are two separate molds that eventually will be put next to one another, a manufacturer can ensure that the texture will transition from one part to the next with a seamless appearance.
Texture and depth flexibility: An additional advantage that laser ablation offers is the ability to have different depths within the same mold. If a user desires two or three different textures within one mold and would like one to be set at a different depth than another, it is as simple to achieve as indicating the depth difference while programming the part.
In which market segments are laser texturing popular?
Some of the biggest players in the packaging, PET blow mold, medical, aerospace, microstructures and automotive markets have started to realize the advantages of this technology. These include the ability to transition to a completely digital environment, 5-axis capabilities and even something as simple as being able to create brand-specific textures.
The plastic bottle/blow mold industry has started using laser texturing technology in interesting and unique ways. Some manufacturers in this segment are creating generic bottle forms and then adding different inserts into the forms to achieve different textures. This enables an infinite variety of bottles from a single bottle form, just by changing the insert.
Bottle manufacturers also can eliminate the traditional steps of milling electrodes and die sink EDMing bottle caps with a laser ablation process. Not only can the laser texturing system put logos and textures on top of the cap, it also is capable of creating ridges along the side due to its full 5-axis capabilities.
For packaging manufacturers, the biggest advantage of laser centers is the ability to impart different contrasts, textures and depths. In addition, another feature that is well suited for the packaging industry is the ability to hit parting lines with the utmost accuracy.
Automotive manufacturers have been some of the most aggressive adopters of laser texturing because there are so many opportunities within the platform. Every manufacturer tries to distinguish their offerings by having different headlights, dashboards, door panels, consoles and even touchscreens, and laser texturing expands the possibilities for differentiation.
One of the largest automotive molds to be textured on a consistent basis is the dashboard. Because the laser is able to work with up to 65,000 different layers instead of just 5-10, manufacturers can make leather grain textures that look and feel like the real thing.
In many cases, headlights require the most unique mold for any individual car model. Not only does every car manufacturer want to a have a different pattern than the competition, but each manufacturer also wants the general consumer to be able to distinguish one style from another. In addition to stylistic choices, headlights also are incorporating more advanced textures due to recent advancements in light bulb technologies. As the bulbs have become brighter, they have become too bright in some cases. In these instances, the lens of the headlight is used to diffuse the light and make the roads safer.