2014 SPE Decorating & Assembly Division Topical Conference
June 10-11 | Ann Arbor Marriott Ypsilanti at Eagle Crest | Ypsilanti, MI | USA
Sessions
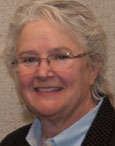
Keynote Speaker
Kathy Minnich, manager for North American Materials Engineering, Ford Motor Company, Decoration Trends and Challenges for Plastics in Automotive Interiors and Exteriors
A sampling of confirmed sessions are provided. Full session listings will be available in mid-February.
Session Abstracts: Decorating
Increasing Pad Printing Productivity and Efficiency
John Kaverman, Pad Print Pros
This paper will look at the seemingly obscure efficiency and productivity mistakes that many companies with pad printing operations unknowingly commit. This paper acts as a guide to conducting an in-house investigation and identifying common mistakes, discusses their potential impact and recommends corrective actions.
Heat-Fused Graphics for Olefin Resins
Jason Brownell, iMIG Systems
The intent of this paper is to discuss the truly permanent nature of a new patent-protected heat fusion process for the transfer of graphics to polyethylene, polypropylene and other olefin products. It will discuss the differences between this heat fusion graphic and other labeling/decorating processes and define the environmental significance of each of these processes.
Effect of Open Air Atmospheric Plasma on the Adhesion of UV-Curable Coatings to Plastics
Paul Mills
Ultraviolet (UV)-cured liquid and powder coatings provide plastic part manufacturers with a number of desirable benefits, including enhanced appearance, improved performance and various process advantages. At the same time, the rapid film formation and densely cross-linked chemistry that characterize UV-curable materials also increase the likelihood of adhesion failures. That these coatings are formulated with little or no solvents makes attaining adhesion even more challenging. This paper examines adhesion problems inherent in UV-curable liquid and powder coatings. It also explores the trade-offs associated with popular methods to mitigate adhesion problems. The conclusion is that atmospheric plasma treatment provides an especially effective means of improving adhesion of UV-curable coatings to a wide range of plastic substrates.
"Smart" Laser Marking – Faster Speed, Better Quality
Scott R. Sabreen, The Sabreen Group, Inc.
The newest generation of laser marking "smart additives" incorporated into polymers is a quantum leap in technology which is both enabling and cost-saving. These advanced material science formulations achieve unprecedented marking contrast, line edge detail and speed on plastics that have traditionally been difficult, if not impossible, to laser mark. Designed for thermal chemical surface reactions, these formulations are ideal for fiber, YAG and Vanadate lasers operating at a wavelength of 1060-1070nm (near infrared spectrum).
Using Decorative Film Laminates with In-Mold Decoration to Increase Design Flexibility
Len Poole, Soliant, a division of AkzoNobel
Consumers continue to place more requirements on OEMs by demanding higher levels of product differentiation, while also expecting low prices. OEMs, in turn, expect their plastic component suppliers to provide them with innovative methods of meeting customer expectations, while under intense cost pressures and operating "lean" and "green". One method of meeting these needs is to use decorative film laminates. This paper will cover how film laminates are made, how to use them and the benefits that can be reaped. Film laminates have millions of potential appearances and allow the use of materials that are difficult to decorate with more traditional coating methods.
Innovations in Plastics Decorating
Ed Crutchley, Crutchley Consulting Limited
The decoration and surface treatment of plastics for esthetic and mainstream functional purposes is the subject of close to 1,000 patent applications a year. About one-third of these relate to the esthetic effects produced. The remainder concern process improvements and functional properties such as abrasion and chemical resistance, antistatic and easy-to-clean properties, antimicrobial behavior and barrier. This presentation presents the main trends across dozens of manufacturing processes and highlights some of the more interesting innovations from the last three years.
The Evolution of Industrial Digital Printing
Chris DeMell, ITW Security & Brand Identity
This session will begin with a brief summary of the introduction of "Industrial Digital Printing". Advancements in technologies and platforms, such as hardware, software, primers and ink development, and LED UV systems and improvements will be discussed, as will new approaches for the decorating technique. As market demands come up against the technology’s capabilities and limitations, where will industrial digital printing go in the future?
Multifunctional and Smart Coatings
Jamil Baghdachi, Coatings Research Institute, Eastern Michigan University
Over the past 25 years, coatings technologies have been influenced by the need to lower Volatile Organic Contents (VOC). More recently, the issues of green chemistry and sustainability have significantly impacted the coatings industry. In addition, there has been growth in research and development and the commercial product generation of coatings which have "stimuli responsive" properties and functions. These products’ multifunctional and smart coatings possess sensory functions and interact with their environment, in addition to having the traditional protective and decorative functions. Examples of such materials include antimicrobial, self-healing, color changing, temperature responsive, superhydrophobic/hydrophilic, degradation sensing, on-off electrical switch, etc. This presentation will focus on technologies and utility of products that can be used as coatings for plastic substrates, as well as future trends.
Vacuum Coating Solutions for Decorative Plastic Surfaces in Automotive Applications
Gerd Ickes, Leybold Optics GmbH
Requirements for decorative surfaces in automobiles are permanently developing and getting increasingly complex. Important aspects are esthetics, durability and cost, as well as additional functions. These often are implemented by coatings. Established technologies for fabrication of such coatings include wet coatings and increasingly combined solutions, such as vacuum-coated or electro-plated surfaces, in combination with finishing clear coats. This paper gives an overview of common vacuum coating technologies. The properties of these coatings are discussed and compared to those of electro-plated and lacquered coatings. Analysis of the requirements for the coatings leads to the conclusion that often a combination of coating properties from different technologies is necessary. While current applications can be implemented by electro-plated or lacquered layers – or combinations thereof, many future applications also may require a combination of lacquered and vacuum-coated layers. Several such product solutions are introduced by means of examples.
Decorating Choices for Automobile Applications: Insert Molding, In-mold Decorating and Hot Stamping
Joerg Bachschuster, Kurz Transfer Products
The presentation will discuss different transfer decorating processes available for plastics automobile parts decorating, including insert molding (widely used in the US), in-mold decorating (still new to the US market, but widely used in Europe) and hot stamping (gaining new acceptance for interior/exterior applications). The paper will discuss how these processes are implemented and when one would be desirable over the other, depending on the specific application.
Modern Water-Dilutable Paints in Industrial Production Application for Plastic Parts
Heiko Klingenberg and Dr. Juergen Rudolph, Diegel Creative Coatings
This presentation will explore the chemistry of water-dilutable 2-K-Paints, with emphasis on the special features of processing, 2 K mixing and dosing units and economic considerations. An outlook will be discussed, as well as applications in the field of fiber composites.
Surface Treatment Solutions for Global Trends in Plastics
Andreas F. Stecher, Plasmatreat USA, Inc., Elgin, IL
This paper examines how global trends in plastics are driving changes in plastics decoration. From eco-chic packaging to automotive weight reduction for better fuel efficiency, these forces are requiring changes in how inks and coatings are applied and processed. This paper surveys major industry trends that are shaping the decorating process, including Eco-Chic plastics, bright metal appearance without chrome, further reduction of solvents, large format digital inkjet, wood-plastic composites and the growth of medical plastics. The paper also examines some of the technical challenges these trends have produced and how surface treatment has been integrated into new and innovative processes that overcome these new challenges.
Session Abstracts: Assembly
Structural Bonding Alternatives for Plastics
Rachel B. Nashett, Henkel Corporation
Industrial adhesives have been used to effectively bond dissimilar substrates, distribute stress loads and vibrational forces and increase the ascetics of structural assemblies. In today’s competitive market, streamlining production and creating better, more reliable assemblies are critical factors to ensuring the success of modern manufactures. Adhesives successfully have been used to displace solvent welding in the plastics industry, join dissimilar substrates and provide structural integrity to a wide variety of products and applications. Typical adhesive applications range from bonding critical medical components to heavy equipment. To ensure the structural integrity of an adhesively joined assembly, appropriate time should be taken to evaluate bond joint design and adhesive selection.
Increasing Requirements for Plastics Joining: Infrared Technology Offers New Possibilities to a Wide Range of Welding Applications
Dave Clothier, FRIMO, Inc.
Infrared welding is gaining importance versus established processes such as vibration and hot plate welding. This non-contact joining method for thermoplastics offers many advantages and is equally well-suited for both small and large components. Solutions have been developed that result in reduced cycle time and make infrared technology a competitive alternative to classic joining techniques used in high-quantity thermoplastic manufacturing processes. Infrared welding technology also satisfies the ever-increasing demands for particle-free operation, such as for air or oil ducting components. It also is exceptionally well-suited for welding high-performance reinforced plastics, such as glass fiber-reinforced plastics and polyamides, which are becoming increasingly commonplace in structural components used in lightweight vehicle applications. The process enables extraordinary weld strength durability, which makes it especially interesting for safety-related applications, while ensuring 100-percent gas-tight welds at the same time. Flexibility is assured, both in the use of the types of materials to be welded, and also in design freedom, which means that it also is possible to weld complex 3D geometries.
Ultrasonic Welding with Automation and Robotics
Udo Skarke, Herrmann Ultrasonics
Shrinking high-volume products and growing multiple-version, lower-volume products, especially in the automotive industry, have forced manufacturers to look for more flexible assembly solutions. In the past, ultrasonic plastic assembly systems were custom designed to assemble specific products. This is no longer acceptable for most manufacturers. Today’s requirements include maximizing flexibility and floor space and minimizing tool change set-up time. Compact ultrasonic actuators with low weights can be easily mounted on robot arms and are thus well-suited for fast and low-energy joining of plastic parts for high-speed automation. In addition, pre-loading the pneumatic cylinder of the actuator saves time – up to one second per weld spot.
Performance of Pressure-Sensitive Adhesive Tapes under Different Strain Rate Regimes
Nigel Pemberton-Pigott, Gene Burger and Dwayne Wasylyshyn, BlackBerry Inc.
The adhesion properties of several pressure-sensitive adhesive (PSA) tapes under different stress levels and associated deformation rates were compared to examine the correlation of standard peel performance to creep and impact performance. Results showed that the typical peel strength testing done at 300mm/min cannot be used to assess the performance at higher (~72,000mm/min) or lower (~0.005mm/min) peel rates. Using different substrates, several PSA tapes were tested in a creep peel-type test and a relatively rigid cantilever-type (mode I opening) impact energy test. Results showed that the creep resistance of a given tape did not provide for a consistent correlation with ranking in impact-type testing. Further, a ranking of peel strengths from available datasheets could not be consistently correlated to a ranked performance of either creep resistance or impact energy. These results suggest that a designer must carefully consider the level and character of the forces created in a joint assembly and may have to consider other adhesive tape performance factors beyond those available on common datasheets.
Benefits of Servo-Driven Ultrasonic Welding for Critical Assemblies
Kenneth Holt, Dukane
Ultrasonic welding is one of the most widely used processes for bonding polymers, valued for its speed, flexibility and low cost. Recently, there has been a call for more controlled and consistent ultrasonic welding processes as part designs become more complex and requirements more stringent, especially in the medical field and for complex packaging applications. Additionally, the processes used to meet these increasing demands must be consistent and repeatable over time. Dukane has worked to meet this demand through the development of a new iQ series servo-driven ultrasonic welder with Melt-Match® technology, which is protected by US and international patents with other US and international patents pending [1, 2, 3, 4]. This study explores the potential benefits of the features solely available with Dukane’s servo-driven welders, such as Melt-Match® (matching welding speed with the melt flow rate of the plastic). A full scale Design of Experiments has been undertaken to identify the relational effects of these speed and distance control features and how they can be used to optimize the welding process. An effort has been made to detail and quantify the improvement to the weld joint based both on previous research, including a joint study with Value Plastics, a large medical device manufacturer, and new experimentation in collaboration with Parker Hannifin.
Balancing Flexible Automation with the Right Assembly Technology Fit for the Product
Tim Gale, TA Systems
Today’s lower volume, yet higher complexity products force manufacturers to look at a wider range of assembly methods than they did a few short years ago. Engineered materials, flexible automation, maximizing capital utilization on lower volume products and budget sensitivity all drive an automation company to have expertise in a wide range of technologies as one technology no longer fits a wide range of applications. Robotic (flexible) automation, interchangeable tooling or dedicated equipment – which is right for the application? Sonic welding, electromagnetic welding, hot plate welding, infrared welding, heatstaking, vibration – which is best suited for a product? This paper will cover some of the decision points utilized to decide which processes and equipment are right for each specific application.
Innovative Welding and Joining Solutions via the Electromagnetic Welding Process
Steve Chookazian, Emabond Solutions
New flexible power-delivery systems are providing a wider range of options for using electromagnetic welding technology for joining of difficult and challenging applications. This paper will cover the principals of electromagnetic welding, including high frequency power delivery and plastic part joint design options. Materials and assembly equipment, including examples of manual and semi-automatic systems, also will be detailed. Application examples will range from small to larger part assembly, including multiple weld lines performed simultaneously. Welding of polyolefins, engineering and filled materials, including dissimilar materials, also will be highlighted within this paper.
Laser Welding – Case Studies of Success
Sophie Morneau, Branson Ultrasoincs
This presentation will explore applications where laser welding was able to succeed when other plastics joining processes were unable to resolve specific issues. The paper will discuss the parameters of the applications, explore the potential joining solutions and outline how laser welding was the best plastics joining choice.
The Continued Relevance of Conduction and Contact Hot-Plate Welding – Don’t Lose Touch with Your Resin Side
Jason Dornbos, Extol, Inc.
Hot-plate welding has come a long way since the days of slow hydraulic- or pneumatic-controlled machines with mechanical tool stops. The integration of servo-driven technology into hot-plate welding machines has provided precise control of position, velocity, force and acceleration. Alternative joining technologies such as laser, infrared and ‘non-contact’ hot-plate welding have been used to avoid the issue of material sticking to heated tooling and to improve flash control. However, these technologies have limitations. It is in times like these when engineers need to be reminded to never lose touch with their resin side. Conduction heat transfer realized in contact hot-plate welding is significantly relevant in the plastics industry today, and ongoing refinement in the process continues to make it the best solution for many plastics joining applications.