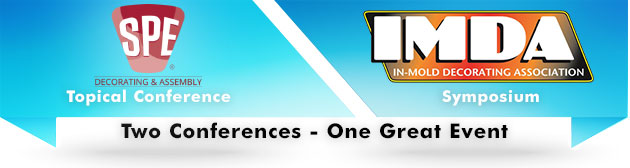
2016 SPE Decorating & Assembly Division Topical Conference and IMDA Symposium
June 5-7 | Franklin Marriott Cool Springs | Franklin, Tennessee | USA
Sessions
Keynote (Opening Presentation)
Current Trends and Future Outlook For Decorative Applications With Automotive Interiors
Andrew Robertson, AkzoNobel Specialty Coatings, North America
Automotive interior styling has evolved into a complex combination of expectations and requirements for texture, appearance, tactile sensation, and longevity. A brief history is provided, followed by a detailed review of current trends with paints and coatings and the challenges to meet user expectations with sustainable and eco-friendly solutions. The discussion concludes with a glimpse of future styling, options, and likely challenges.
Session Abstracts: Decorating
Expanding Applications for Pad Printing
John Kaverman, Pad Print Pros
Pad printing has evolved from being a mysterious, labor intensive, messy production afterthought to a robust, technologically advanced, automated process. This paper will focus on some of the machinery, methods and materials used to maximize the efficiency in automating part acquisition, orientation and loading, pre-treatment, high-speed pad printing, drying, curing, vision inspection and more.
Plasma Surface Treatment for a Clean Surface to Attain Adhesion
Andy Stecher, Plasmatreat North America
Proper adhesion requires a clean surface. Even small amounts of contamination can cause a coating, ink, or adhesion to fail. This paper reviews the advantages and disadvantages of various cleaning approaches, and suggests that plasma surface treatment is an effective, safe, environmentally-friendly, and cost-efficient means of cleaning parts. Plasma cleans by altering the chemical composition of common organic soils and contaminants. Thus, cleaning with plasma surface treatment is particularly well suited for applications where the cost and consequences of adhesion failure are high and where greater rigor in achieving a higher standard of surface cleanliness is warranted.
Science of Permanent Printing on Flexible Olefins
Jason Brownell, Polyfuze Graphics Corporation
This paper will discuss a new patented process which fuses together the transfer of graphics to flexible olefin materials. This process involves heating the graphic and olefin product simultaneously and fusing them together without the use of adhesive. Although this technology uses standard heat transfer equipment it requires only a fraction of the pressure required in a traditional heat transfer application with only a slight adjustment to machine settings. The difference between other plastic decorating technologies as they relate to flexible materials will also be discussed. The scope will focus on olefin based materials such as TPR, TPV, SEBS, TPO’s, TPE’s with added content to include non-olefins material such as flexible PVC.
In-Mold Decorating with Laser Etching
Dan Haas, Serigraph
The successful implementation of laser etching with in-mold decorating requires knowledge of the material science and laser function. This presentation will discuss the design challenges with laser etching and the in-mold process, the ability to maintain tight graphic registration, how IML can provide features difficult to replicate with traditional paint and laser etch, as well as how utilizing in-mold and laser etch can provide technical benefits for such things as backlighting.
New Technologies for Cylindrical Part Screen Printing
Scott Frey, OMSO North America, Inc.
Today’s container decoration packaging operations can now be designed as a complete manufacturing cell. Containers can be decorated directly from molding operations through unscramblers and high-speed feed and handling systems… screen printed, labeled, inspected for print omissions, leak detected, accepted or rejected, then robotically handled and packed. Leading edge screen printing technology includes precision servo-driven machine components, precision camera registration, quick changeover times to allow short-run SKU’s, robotic feeding and exiting belts, and independently programmable print stations allowing specific parameters for each bottle.
Reactive Gas Technology to Activate Plastics for Decorations
Prakash Iyer, InHance Products
Commodity polymers, such as polyethylene and polypropylene, often are chosen over engineering or high-performance polymers due to factors that include lower costs, availability and broad processing latitude. These materials, however, often exhibit very low surface energy, which creates poor adhesion characteristics and leads to poor printability, adhesive assembly, composite production or metallization. There are a number of techniques to overcome these drawbacks through the application of various forms of energy to temporarily activate the surface for subsequent processing, including flame, plasma and corona treatment. Another effective means to activate surfaces is the use of reactive gases to impart permanent increase in surface energy. This paper will discuss the fundamental features and industrial applications of gaseous surface activation of polymers using InHance Technologies’ Reactive Gas Technology™ (RGT).
Insert Moldable Films with Incorporated Anti-Reflective, Abrasion and Moisture Resistant Coatings
Luis Beltran, Nagase America
In mold plastic lens assemblies are increasingly being used for automotive center stacks and similar applications. In order to achieve required optical and functional performance required for these applications the addition of post operation coatings to provide scratch resistance and anti-reflection characteristics has become the norm. This paper will discuss new in mold films that incorporate these features into the film without the expensive and time involved in post molding operations allowing production of a finished part after screen printing and molding. Performance characteristics and test data will be presented on various grades of film.
Digital Solutions for Industrial Product Decoration
Chris DeMell, ITW SBI
Since the emergence of digital inkjet as a new option for industrial product decoration, companies have searched for ways to incorporate the unique advantages that the technology offers. A review of the evolution of digital inkjet will be covered as well as unique strategies to address industrial applications. Areas such as substrate variability, environment, regulatory compliance, abrasion resistance, color matching, and 3D product decoration will be addressed. In addition, specific market needs will be looked at to show how digital is being incorporated into today’s industrial markets.
FDA-Approved Additives & Fiber Lasers Advance Laser Marking
Scott Sabreen, The Sabreen Group, Inc.
Fast speed, superior contrast and cost-savings are among the significant benefits of incorporating novel FDA-approved additives into polymers for laser marking. Chemical additive breakthroughs produce jet black and light-colored contrast both “on-the-fly” and during secondary opera¬tions. The advancements in nanosecond Ytterbium Fiber lasers have been instru¬mental to the rapid development of the newest generation of FDA-approved laser additives.
Advantages of UV LED Curing Printed and Assembled 3D Plastic Parts
Jennifer Heathcote, Phoseon Technology
The adoption rate of UV LED curing technology for 3D printed and assembled parts is an upward trend driven by economic, process, and performance benefits. Companies willing to investigate the state of the technology and qualify it for their specific application needs are increasingly making the switch. This paper will highlight the current state and advantages of UV LED curing across a range of market applications including digital inkjet, screen, dry offset, pad, and dispensed adhesives.
2D/3D Hot Stamping, In-mold and Insert Molding Applications in Automotive and other Industries
Matthew Small, Kurz Transfer Products
The presentation will discuss different transfer decorating processes available for plastics parts decorating, including 2D and 3D hot stamping (gaining new acceptance for exterior/interior applications), in-mold decorating and insert molding. The paper will discuss how these processes are implemented and when one would be desirable over the other, depending on the specific application.
In-Mold Thermoformable Laminates for Handheld Design
L. Coubrough, Max Aicher North America Ltd., Hamilton, Ontario, Canada
D. A. Wasylyshyn, Independent Consultant, Waterloo, Ontario, Canada
The use of thin, glass-reinforced laminates in smartphone device construction will be discussed with the continued trend to thinner constructions while maintaining antenna compatibility as well as rigidity for mechanical robustness. The incorporation of such laminates on previous smartphone designs will be discussed in terms of the various manufacturing process steps and unique challenges, including the issues with incoming material defects, some of which are inherent to the lamination process. The laminate material was also analyzed using differential thermal calorimetry (DSC) techniques in order to understand its response during the manufacturing processes. The cosmetic and functional defects that are possible in the final insert-molding and decorating of the laminate will be discussed along with known root causes and corrections.
Replacing Decorative Electroplating: Methods, Challenges, and Resources
Josh Mangum, Mustang Vacuum Systems
Electroplated chrome is a commonly used decorative finish in a variety of markets including automotive interiors/exteriors, appliances, and hardware. Due to environmental concerns plated finishing processes are coming under scrutiny by regulators, forcing manufacturers to seek alternative solutions to decorative plating. Many manufacturers are currently developing Paint-Metal-Paint (“PMP”) processes as a cost effective solution for replacing decorative chrome plating. The PMP process uses liquid or powder paints as a protective coating that surrounds a vacuum deposited metal color layer. This paper will discuss the transition from electroplating to PMP solutions and identify many common PMP integration pitfalls and how to avoid them.
Session Abstracts: Assembly
Understanding Adhesives and Their Chemical Resistance
Austen Williams, Henkel Corporation
With the advancements made in modern manufacturing, adhesives are becoming not only a key product for industrial assembly but also a key product for chemical and corrosion resistance. Adhesives are capable of mating dissimilar materials, providing full stress distribution along the bond line, and sealing the bonded assembly from chemical exposure. While an adhesive is capable of fulfilling all three of these requirements, the chemical resistances of Henkel’s industrial adhesive line vary by application and chemistry. Before choosing a product that will be exposed to a chemical it is important to first identify the chemical and the parameters that the adhesive will be exposed to.
Importance of Impact Resistance in the Adhesive Selection Process
Nathan Landsman, Henkel Corporation
The paper will focus on the importance of impact resistance when selecting an adhesive. It will briefly describe the process in selecting an adhesive based on application, adhesive characteristics and tie in how impact resistance is a key element in this process. It will go on to describe what impact testing involves and how it is measured. This will be followed by an analysis (with graphs and data) of the impact resistance of different chemistries and some of the common misconceptions involved with them. The conclusion will re-iterate why impact is important in the adhesive selection process and qualification of an adhesive. Chemistries that will be discussed in this paper include: cyanoacrylates, epoxies, polyurethanes, acrylics and modified silane polymers.
Staking Showdown: Comparing the Process and Performance of Plastic Staking Methods
Kelly Binnendyk, Extol, Inc.
Plastic staking or 'heat staking' is a common joining method used to retain components to a thermoplastic substrate. Several different technologies are available today that accomplish this task. This presentation compares three of these plastic staking processes: ultrasonic staking, hot-air staking, and infrared staking (InfraStake). The strength of the stake, the repeatability of that strength, and the cost of the equipment is explored for each technology.
Utilizing Advanced Melt Flow Controls of Servo Driven Ultrasonic Welding Equipment for Critical Applications
Ken Holt, Dukane
Ultrasonic welding of thermoplastics is widely used by many industries to fuse together two parts in a short time without additional consumables. The development of servo-driven ultrasonic welders introduces unique levels of control. This study pursues previous research and investigates the capabilities of servo-driven welders to produce stronger welds. It focuses on developing a more robust and better controlled joining process for medical devices that increases the strength and reliability of welds without fully collapsing the joint or creating excessive weld flash. Experiments were completed in which the weld velocity was varied, and the resulting strength and appearance of the welds were evaluated against the intense requirements of the medical industry. Analysis of weld cross sections suggests that higher weld strength was associated with a linearly increasing weld velocity profile.
Cost Effective - Versatile Solutions using the Electromagnetic Welding Process
Steve Chookazian, Emabond
Welding via high frequency electromagnetic energy has been in commercial use for decades. The process is often considered as an ideal method for critical high performance applications where the cost of failure of the weld is of great concern. The tradeoff historically has been that the perceived high cost of using the process. Recent developments in the technology and approach to equipment and tooling as well as the consumable material economics have significantly reduced the cost to implement this reliable, versatile, non-violent plastic assembly method. The emphasis of this paper will highlight examples of much lower cost, versatile solutions using electromagnetic welding as well as provide an overview of the technology and thermoplastic materials often joined including dis-similar materials and joint design examples.
Understanding the Benefits of UV Curable Screen Printing Technology
Curt Baskin, Sun Chemical Corporation
Under the definition of Hi-Tech Graphics, UV Curable screen printing inks are used for decorating a variety of 3D parts, including automotive, appliance and medical parts. This paper will discuss UV curable screen technology used for these market segments. It will discuss the advantages of UV curing screen inks, processing UV curing screen inks correctly, do’s and don’ts for UV screen, as well as proper UV ink handling and storage.
Clean Joining Technologies
Craig Birrittella, Branson Ultrasonics
The discussion will review a group of technologies that are used in the plastics joining field called “Clean Joining Technologies”. The technologies in this group include: Infrared, Laser and an Infrared & Vibration Welding hybrid technique. The discussion will focus on the fundamentals of each process, the advantages and limitations of each, when to choose one over the other and typical applications in the market.
Laser Welding vs. Other Joining Processes
Jim Greene, LPKF Laser & Electronics
Laser plastic welding is well suited to work with most any plastic joining need. However, each joining method has its own set of advantages and disadvantages. This paper will walk you through the pros and cons of each method, to help you determine which process is best for your application.
Session Abstracts: In-Mold Decorating Association
Digital Printing of In-Mold Labels
Bob Travis, Inkworks Printing LLC
Digital printing has come of age and it is used increasingly for conventional product packaging and product decorating. When digital printing is combined with in-mold decoration new levels of product value can be created. This paper explores how variably imaged in-mold decorations can add product functionality, increase brand and product appeal to consumers and generate new levels of customer engagement. These concepts will illustrate how digital IML is closely related to the thinking behind the Internet of Things.
“We’ve come a long way…” Knowledge Gained/Lessons Learned
Pat Tully, DuraTech Industries
Knowledge Gained/Lessons Learned in our nearly 20 years of IMD experience in primarily the automotive and appliance markets. The importance of concurrent design, early involvement and allowing enough time for development are the major topics of focus. In addition, we will discuss forming guidelines and the cost impact of preforming a label vs molding a flat label. Other topics will include graphic position guidelines to avoid distortion and wash, molding guidelines and other lessons learned.
Special Effect Inks and Coatings Properties and IML Application Requirements Usually Don’t Overlap
Jim Wittig, ACTEGA
The graphic arts world over the last 15 years continues to evolve into more sophisticated graphic designs. This has been led by innovation in chemistry enabling special effect coatings and inks as well as new printing techniques and equipment. Most of these exciting special effects technology have not broken into IML applications. This is because the high performance and functional requirements on the surface of IML labels require coatings and inks designed to withstand the demands of in-mold labeling first and not impede productivity of the molding process. A discussion of the technology, both chemistry and printing methods, behind special effect inks and coatings will be contrasted to the design requirements of IML labels. Commonly used effect inks and coatings include Soft-Touch, Strike-Thru Matte/Gloss effect, 3D high profile printing Thermochromic, Glow-in-the-dark, Glitter and brilliant Metallic foil like inks. Design criteria for IML applications include, lay-flat and coating shrinkage properties, surface electrical properties, COF, abrasion and heat resistance and in many food safety applications.
Overcoming IML Cavitation Limitations
Jordan Robertson, StackTeck